11: Reproducing Your Work
The fact that you are interested in DTP (and presumably you are since you are reading this book!) indicates that you are involved in some way in the world of publishing. Of course it may be that you delight in preparing text and devising page layouts simply to satisfy some innate whim. However, it is far more likely that you are interested in using your computer system for some genuine publishing purpose such as the production of newsletters or magazines for your club, school or church or letterheads, forms or promotional literature for your business.
If so, you will almost certainly want many copies of the wonderful artwork that comes oh-so slowly out of your printer. Let us consider how to do this. After all, the verb publish literally means "make public", the ideal being to let everyone have a copy who would like one.
There are three main methods of producing multiple copies: using your computer printer, using a photocopier and using offset litho printing. The method you choose depends partly on the quality you want and the urgency with which you want it. But by far the most significant factor is the number of copies you require.
How many copies?
If you want only one copy then you need look no further than your existing computer printer. The single copy that it produces will suffice, and if you want more than one, but only, say, two or three copies of a document that is no more than four or five pages long, then you may be content to wait a while for your computer system to churn them out individually.
Photocopiers
For quantities of up to about 500 copies, the most economic method of reproduction is to use a photocopier. If you run a business you may already have one. If you are in employment, your employer may grant you access to one at a modest cost, especially if the job is charity related. Failing that, every High Street nowadays has one or more "instant print shops" offering photocopying facilities at a competitive price.
There are several distinct sorts of photocopier, but the system that has now all but replaced its rivals is known technically as xerography. A drum is given a positive electrostatic charge. A lens projects on to the surface of the drum an image of the document being copied. Where light falls on the drum, ie in the white parts of the image, the light destroys the electrostatic charge. But in the dark parts of the image, the charge remains. The drum is then dusted with powdered ink called toner which bears a negative charge. Since opposite charges attract, the toner collects on those areas of the drum which are positively charged, and which correspond to the black areas of the image. The drum now contacts the paper, transferring the toner image to it. The paper, which is ordinary plain paper, is heated. This melts the toner which now becomes firmly stuck to the paper and goes hard on cooling.
The drum is the heart of the xerographic process. In early machines it was a frequent cause of problems in photocopying since any blemish on its delicate surface was likely to leave a mark on each copy made. In many modern machines, however, the drum is itself a part of the toner cartridge and is discarded and replaced when the toner cartridge is changed.
Nowadays, the quality of reproduction is generally excellent. It is far superior to that obtainable as recently as five years ago. Even half-tone illustrations can, with care, be reproduced quite acceptably. Photocopiers vary widely in the facilities they offer. The most sophisticated office machines can handle sheets up to A3 size copying on to both sides simultaneously at speeds of up to one copy per second. Some automatically collate and even staple multi-page documents. Many offer a choice of colour of reproduction by means of interchangeable toner cartridges. Most offer "zoom" facilities allowing enlarged or reduced size copies. This type of machine is favoured by the instant print shops since it is ideal for short-run work, the kind of work in which a DTP user is most likely to be interested. At the opposite end of the price scale are small personal copiers. The simplest generally take only A4 paper and offer no "zoom" facilities.
You may be able to set the machine to produce up to 9 or perhaps 99 copies. Some of these use interchangeable toner cartridges giving a choice of colours. For producing small numbers of single-sided, single- colour copies, such a machine would be perfectly adequate. A run of 250 double-sided copies on such a machine would, however, be distinctly tedious.
Between these two extremes are many machines offering intermediate levels of sophistication. The Canon PC-7 which I use is a very compact machine which, remarkably in a machine at its price, features automatic exposure control (which can be over-ridden) and zoom from 70 to 122 per cent in steps of 1 per cent. Runs of up to 99 copies can be pre-set, although the auto-feed mechanism is not reliable- many long runs being terminated with a jammed sheet before completion! Toner cartridges are available in four colours besides black and the quality of reproduction is impeccable. Mine is used mainly for single copies and runs of 20 to 50 copies.
The quality of photocopying is affected by the type of paper used. The familiar rule "you gets what you pays for" applies here as in most other areas of life. Inferior paper gives inferior results. You cannot expect fine detail, for instance, on paper having a coarse texture. On a photocopier with automatic feed the handling characteristics of the paper become important. My personal attempt to conserve planet Earth's limited resources by using what claimed to be 100 per cent recycled photocopier paper proved catastrophic. Despite the worthiness of the cause I was compelled to resort, reluctantly, to "new" material. Don't be afraid to shop around and try different makes. You may find that a different brand gives a dramatic improvement at little or no extra cost.
In buying a photocopier or even finding a suitable machine in a print shop watch out for one problem. Machines fitted with zoom sometimes cause distortion, the vertical lines tending to slew clockwise. This is particularly noticeable if you photocopy a photocopy since the effect is cumulative, each generation slewing the verticals further. The test is to photocopy a piece of graph paper and then photocopy the copy. Superimpose the second-generation copy and the original and hold them up to the light to see if they correspond.
Offset litho printing
For runs of 500 or more copies you may find that it is cheaper to use offset litho printing. Unless you work in a printing shop, you are unlikely to have access to such a machine and so you will have to use a commercial printing company.
Offset litho is now the most widely used printing technique. The page being printed is copied on to a flexible metal (or sometimes paper) "plate" by a process similar to photocopying. In fact ordinary photocopiers arc sometimes used for this purpose. The image on the plate is still the "right way round". The plate is then fixed to a drum, commonly called the "cylinder", which contact'' a rubber "blanket" roller which in turn contacts the paper
Lithography uses the principle that oil and water do not mix. The ink is oil based and therefore immiscible with water Ink and water are separately applied to the entire surface of the plate cylinder before it contacts the blanket roller. On the surface of the plate, however, the ink is attracted to those areas where the plate is dark and water is attracted to those where it is light. A temporary mirror image in ink and water is formed on the blanket roller. When this mirror image transfers itself to the paper, it creates a right-way-round image on it. One of the advantages of offset lithography is that its rotary action lends itself to high-speed work. On earlier letterpress machines it was necessary to insert the paper, "stamp" the image on to it, then remove the paper. This was a reciprocating start-.stop-start process. In offset litho the paper, either as separate sheets or as a continuous roll called the "web", keeps moving like a never-ending stream of clothes through a mangle,
The cost of litho printing will include elements towards the cost of the paper and ink and also of the plates. Since the cost of the plate and its processing i? the same no matter how many copies are made from it, the unit cost per copy will fall as the print run gets longer.
Preparing work for photocopying or printing
The preparation of work for reproduction, whether by photocopier or litho, is essentially the same. Both processes start, so far as we are concerned, with the "fair copy" which your DTP system has produced.
Photocopiers and litho printers are effectively "digital" machines in that they see matters in terms of black (or whatever the toner or ink colour) and white (or whatever the paper colour). They cannot reproduce intermediate shades. This has two important repercussions for DTP users, both of which can be summarised as "your sins will find you out!".
Firstly, if you use a dot matrix printer with a well worn ribbon you cannot expect good results. For instance, if you attempt to print a solid black area on a dot matrix printer with a worn out ribbon the result will be a mass of tiny black dots separated by diminutive but nevertheless real areas of uninked paper. It may appear like a grey mass to you and you may be tempted to think that by turning the photocopier (or platemaker) exposure control to "dark" you will get solid black copies. You won't. The copies will look no better than the original and probably considerably worse. If you are doing an important DTP job that must look good, the golden rule is fit a new ribbon first! If you are one of the many computer users who insist on using printer ribbons down to the last molecule of ink, then keep the old one in a safe place and put it back in the printer after you've printed out the DTP job.
Secondly, half tones (such as photographs) should normally be screened. This is the process which converts areas of solid grey or colours to patterns of tiny black dots on a white background which the photocopier or litho equipment can reproduce satisfactorily. Screening demands access to professional printing equipment. Your friendly neighbourhood print shop will certainly do it for you if he is also doing the printing. He may be willing to do it if you are going to do the reproduction work yourself on a photocopier. Work out the space that each item being screened will occupy and in your layout draw a rectangle of the appropriate size in the right place. Print inside it a clear label such as "Figure 3 here" or "Photo of Chairman here" for identification purposes. Also, whenever you send photographs to a printer, make sure that they are correctly and clearly labelled on the reverse. If there are several photos of personalities, remember that although you personally know which is Joe Bloggs and which is Fred Nurk, the printer may not. Even clearly identified photographs sometimes get interchanged by printers.
You may get away without screening if:
- the picture has already been screened, eg if it was cut out of a newspaper and pasted in place (in which case you may technically be guilty of breach of copyright if you reproduce it without permission)
- the picture contains abundant tiny detail (in which case it has effectively screened itself)
- the picture was reproduced on a high-resolution (300 dots per inch or better) printer out of !Draw or !Paint in which case the software itself provides a somewhat coarse level of screening.
Try to avoid cutting and pasting of the literal variety. In both photocopying and litho work the edges of pasted pieces often become visible as faint lines which are unsightly. One of the great benefits of DTP is that the software equivalent of cutting and pasting leaves no such marks!
For very high quality work, where the output of even a laser printer would not be adequate, there is a further option available to you. This is to send the page data to a printing company for setting on a linotron or other high-definition typesetting machine. Many of these operate at about 1200 dots per inch and most require their input as PostScript files. A PostScript driver is supplied with RISC OS. From its icon menu select the option of sending its output to a file on disc rather than to a PostScript printer.
Full Colour work
!Draw provides by default black, white, six intermediate shades of grey and eight colours which you can use on the screen to make up beautifully coloured pages of text, drawings and sprites. But, unless you have a colour printer, when you print out coloured matter your printer will print only in monochrome, using dither patterns to represent coloured or grey matter. And watch out for bugs which cause black text to become "dithered" adjacent to non-black text.
If you have a colour printer you may be able to print in several colours, producing a tolerably accurate full-colour representation of the screen display. Reproducing these coloured printouts is, however, a complex matter. If you require only very few copies, it is best to simply let your colour printer chum them out. If you require more and if it is imperative that the copies faithfully reproduce the colour original that came off your printer, you can use colour photocopying.
The alternative is colour litho. You will be charged about £75 for "colour separation", that is separation of your artwork into its red, yellow, blue and black components. You will also be charged for four plates, one for each colour. The print run will require four lots of ink and careful alignment (the technical term is "registration") to ensure that the separate colours are accurately superimposed. So expect a hefty bill! Some small printers, incidentally, do not themselves handle four-colour work, they subcontract it to a larger printer. This will further add to the bill as both printers will, not unreasonably, aim to make a profit from the job.
Spot colour
If you want to add colour to your work in a more cost-effective manner, you can use what the printing trade calls spot colour. This is the use of a limited amount of a second colour (or even second and third colours) on an otherwise black-and-white page.
Design your page as though it were monochrome. When you have completed your layout work, but before you have printed it out, save it to disc in the normal way. Now examine it on screen to see if there is a heading or a piece of graphics that would look good in a different colour. Another possibility is a coloured tint behind a drawing. Use the colours sparingly. More than two or three items in colour on an otherwise black-and-white page can look untidy.
Now, if you are adding a coloured item (such as a block of tint) to the page, add it as though it were in black, and save the page again under its normal filename.
If you are changing items from black to colour, delete them from the page. The screen should now show only those items which you want printed in black. Print it out and save it to disc under a different filename.
Next, reload the original and delete everything that is to be printed in black so that only the coloured item(s) remain in their original places. Print it out (in black!) and save it to disc under, yet another, different filename.
You now have two printouts, one of the black matter and one of the coloured matter. And you have the page saved in three different files, one "complete" one, one showing only the black matter and one showing only the coloured matter.
If you are going to photocopy the material, photocopy the black matter first in the normal way. Next, change your toner cartridge to the required "second colour". Then photocopy the coloured matter, passing the black copies back through the machine so that the coloured matter is superimposed on the black. With a photocopier, it is impossible to get registration accuracy better than about 1 millimetre. This means that adding second colours to graphs or diagrams is not really practical. But for headings or coloured boxes around black headings, registration errors up to 1 mm are unlikely to be noticed.
For litho printing you will need to present your printer with the two sets of artwork, one representing black matter and one representing colour. It will normally be obvious which is which, but you will need to agree with the printer which second colour you wish him to use. You can expect significantly better registration than in photocopying so that use of second colours in graphics is feasible. You will be charged extra for the second colour, of course, since a second plate will be needed and the printer will need to make a second print run if he does not have a two-colour press. It will cost extra, but not nearly so much as four-colour work.
It may appear that there is another, simpler, way in which your computer can produce "colour separations". If you compose your page knowing from the start which items will use spot colour, let us say all headings will be in red, you can select red on the screen for your headings, leaving all the black matter in black as normal. Then, using the colour-change facilities on the palette, redefine the red headings to white and do a printout of the remaining black material. Restore default colours and then redefine black to white and red to black. A printout now will consist of the red matter printed as black. Let me assure you that this process does not work. The two printouts will be identical, the black matter appearing in normal black and the red in a dither pattern representing red. This is because the palette only affects the screen display. For printing, the screen display is ignored and the colour data is derived from that in force when the objects were created.
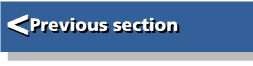 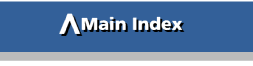
|